jstanfield103
Blackhawk
Hay Guy's/ Gal's
I have been away from Ruger for a long time now. Really been working on building up my Lever action rifles in most of the calibers that interest me. But after that I have been buying some revolvers to go with my rifles. Recently went looking for a 44 Mag in a revolver and looked at two Ruger Super Blackhawks (wanted single action) one with the 4.2" barrel and one in a Hunter model. I figured on the Hunter model due to the weight and length, and wanted to fit it with a Red Dot along with using factory sights. I brought her home fitted her up with the Red Dot and went to clean her up. Upon opening the Loading Gate, wow took some good force to open it. Really had to force it opened. Took it apart and discovered that the frame next to the pivot point was not really machined very well and was cut at a little angle to where the gate would rub and scrape against that bad cut. Little file work and all is well, gate still a little stiffer than my Vaquero though. But I did order a reduced gate spring for it to help that. Also while taking her apart for the gate problem I noticed that the Transfer Bar, the pin that goes into the trigger was not a round pin but a half moon pin. Knew this could not be right. You could see where it was ground down. Don't know what they were thinking on assembly of this revolver. I wrote Ruger yesterday and asked for them to send me another Transfer Bar. I will see what they say about it. Really kind of disappointed in Ruger Quality the last few guns of theirs that I have purchased.
Took her to the range today to sight her in and see what she does. Very happy with the way she operates and she is very accurate. All though I am disappointed in Ruger quality I am very happy with the way she shoots. The transfer bar although is at an angle to the firing pin she did work. She is at an angle due to that half moon pin. I went ahead and ordered a new transfer bar off of ebay and will keep the one Ruger sends me, if they due as a spare.

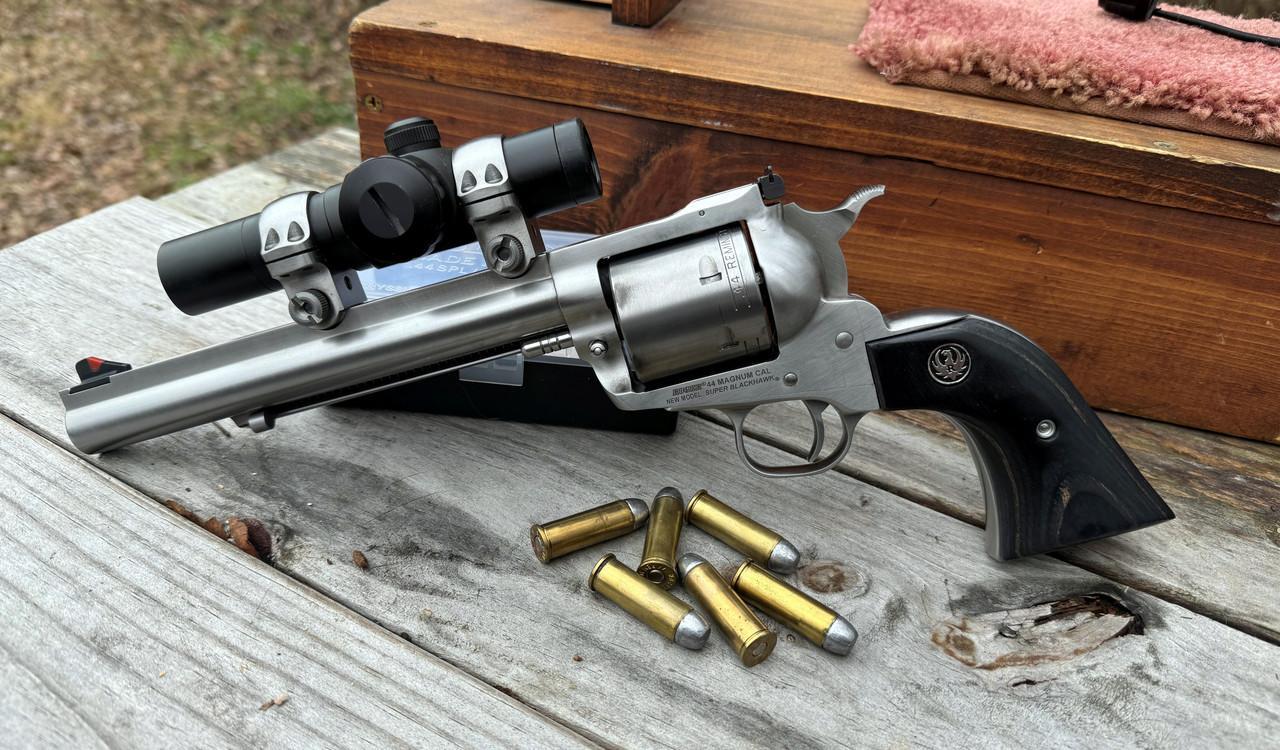
Transfer Bar Pin part showing
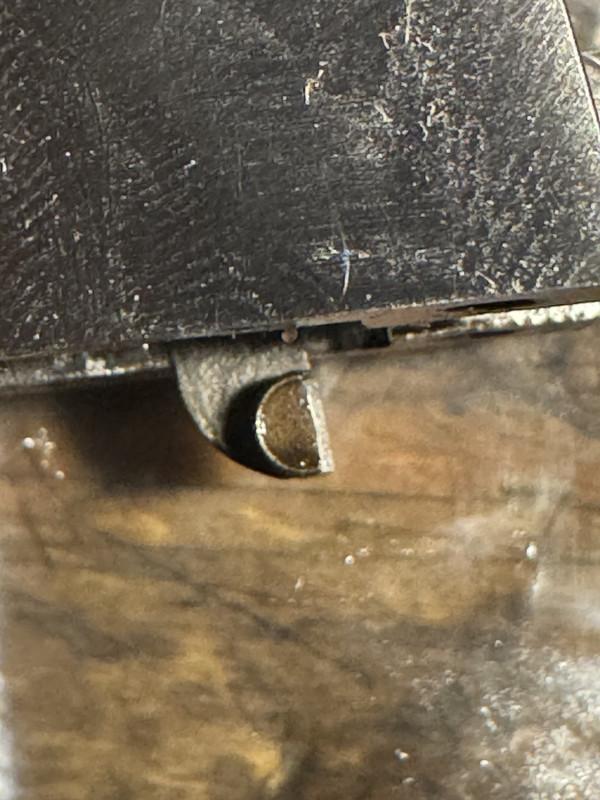
I have been away from Ruger for a long time now. Really been working on building up my Lever action rifles in most of the calibers that interest me. But after that I have been buying some revolvers to go with my rifles. Recently went looking for a 44 Mag in a revolver and looked at two Ruger Super Blackhawks (wanted single action) one with the 4.2" barrel and one in a Hunter model. I figured on the Hunter model due to the weight and length, and wanted to fit it with a Red Dot along with using factory sights. I brought her home fitted her up with the Red Dot and went to clean her up. Upon opening the Loading Gate, wow took some good force to open it. Really had to force it opened. Took it apart and discovered that the frame next to the pivot point was not really machined very well and was cut at a little angle to where the gate would rub and scrape against that bad cut. Little file work and all is well, gate still a little stiffer than my Vaquero though. But I did order a reduced gate spring for it to help that. Also while taking her apart for the gate problem I noticed that the Transfer Bar, the pin that goes into the trigger was not a round pin but a half moon pin. Knew this could not be right. You could see where it was ground down. Don't know what they were thinking on assembly of this revolver. I wrote Ruger yesterday and asked for them to send me another Transfer Bar. I will see what they say about it. Really kind of disappointed in Ruger Quality the last few guns of theirs that I have purchased.
Took her to the range today to sight her in and see what she does. Very happy with the way she operates and she is very accurate. All though I am disappointed in Ruger quality I am very happy with the way she shoots. The transfer bar although is at an angle to the firing pin she did work. She is at an angle due to that half moon pin. I went ahead and ordered a new transfer bar off of ebay and will keep the one Ruger sends me, if they due as a spare.

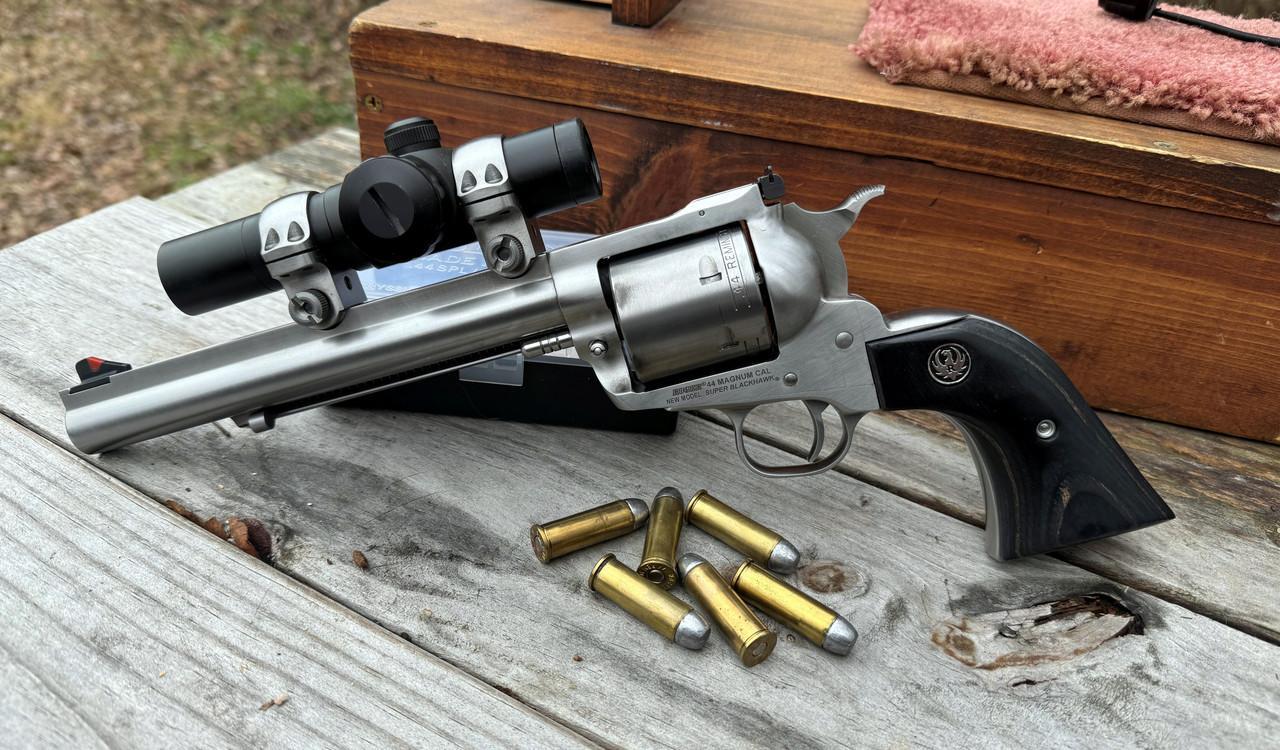
Transfer Bar Pin part showing
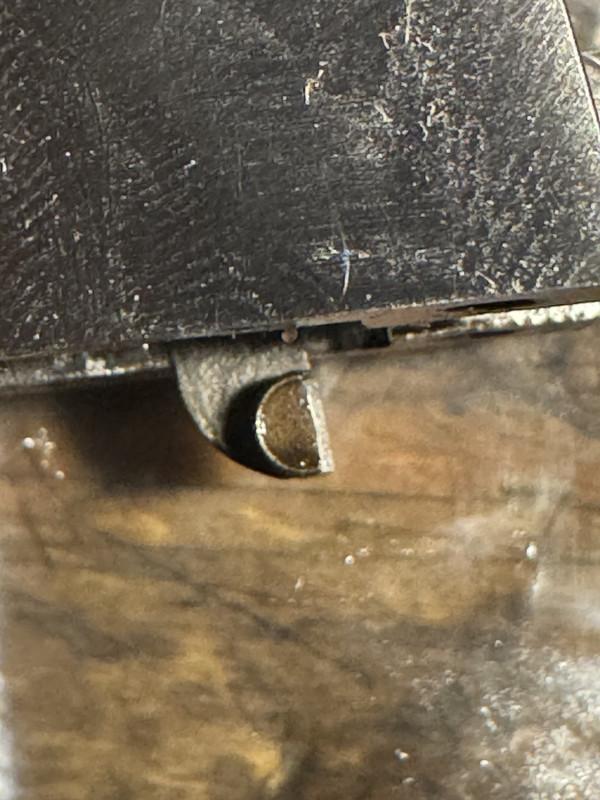